Cathodic Protection for Ships, Boats, and Vessels
- ESC Group
- 10 de nov. de 2022
- 3 min de leitura
ESC’s cost-effective and high-quality corrosion protection solutions applies not only to the preservation of structural parts of marine facilities but also to sea-borne vessels and navigation equipment. Our coating and anode products and designs are also ideal to maintain the integrity of ships, boats, barges, navigation aids, and others.

Supplementary to protective coating systems in mitigating rust, sacrificial anodes or cathodic
protection are installed at the immersed sections of vessels especially the external surface of the hull and internal surfaces of tanks containing seawater. Zinc, aluminum, nickel, and magnesium as less noble, most active metals are used as anodes. Zinc and aluminum however, are more utilized in marine and shipping industry. Both zinc and aluminum anodes are produced by ESC, in different sizes and configurations.
Ship or boat anodes are classified according to material, shape, size, and mounting method.
Anode Material
There are two parameters that measures the performance of cathodic protection: 1) Closed Circuit Potential (the measure how a sacrificial anode is readily corroded); and 2) Electrochemical Capacity (the rate at which the anode material is consumed).
Aluminum. Closed circuit potential = -1.10 Volts; electrochemical capacity = 2,000 Ah/Kg
Zinc. Closed circuit potential = -1.05 Volts; electrochemical capacity = 780 Ah/Kg
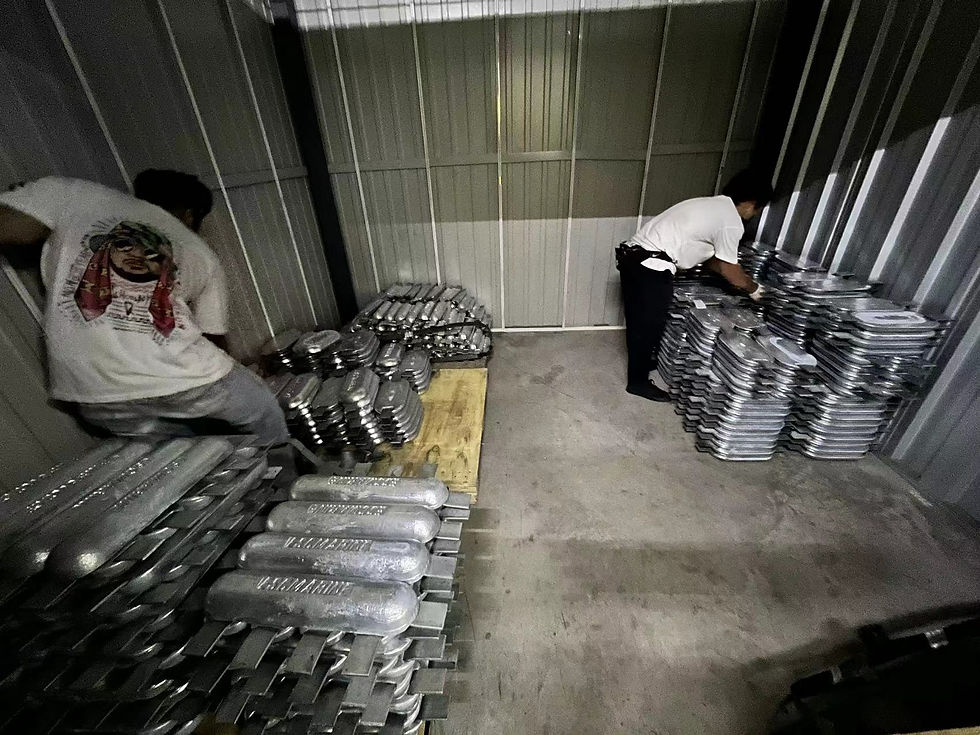
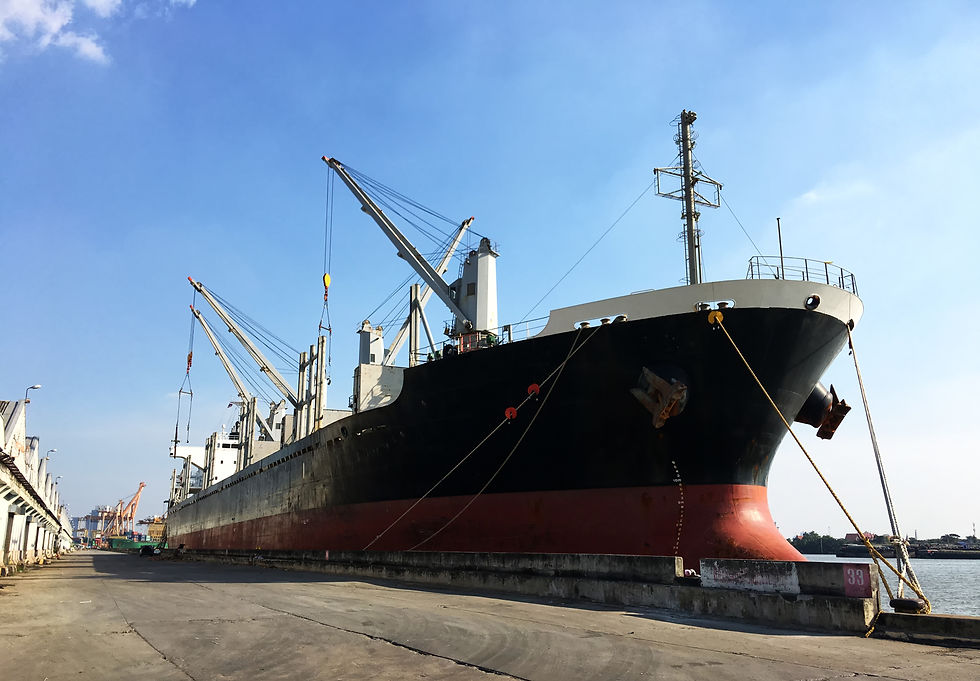
Aluminum anode is more negative than zinc, thus activates more instantly for the galvanic process. It also has a higher electrochemical capacity value making it to last longer considering the same volume.
Zinc however, are found to be more effective in areas with lower oxygen level and higher bacterial activity and considered the traditional cathodic protection metal.
Anode Shape
Anodes comes in different shapes as required by different installation restrictions and conditions.
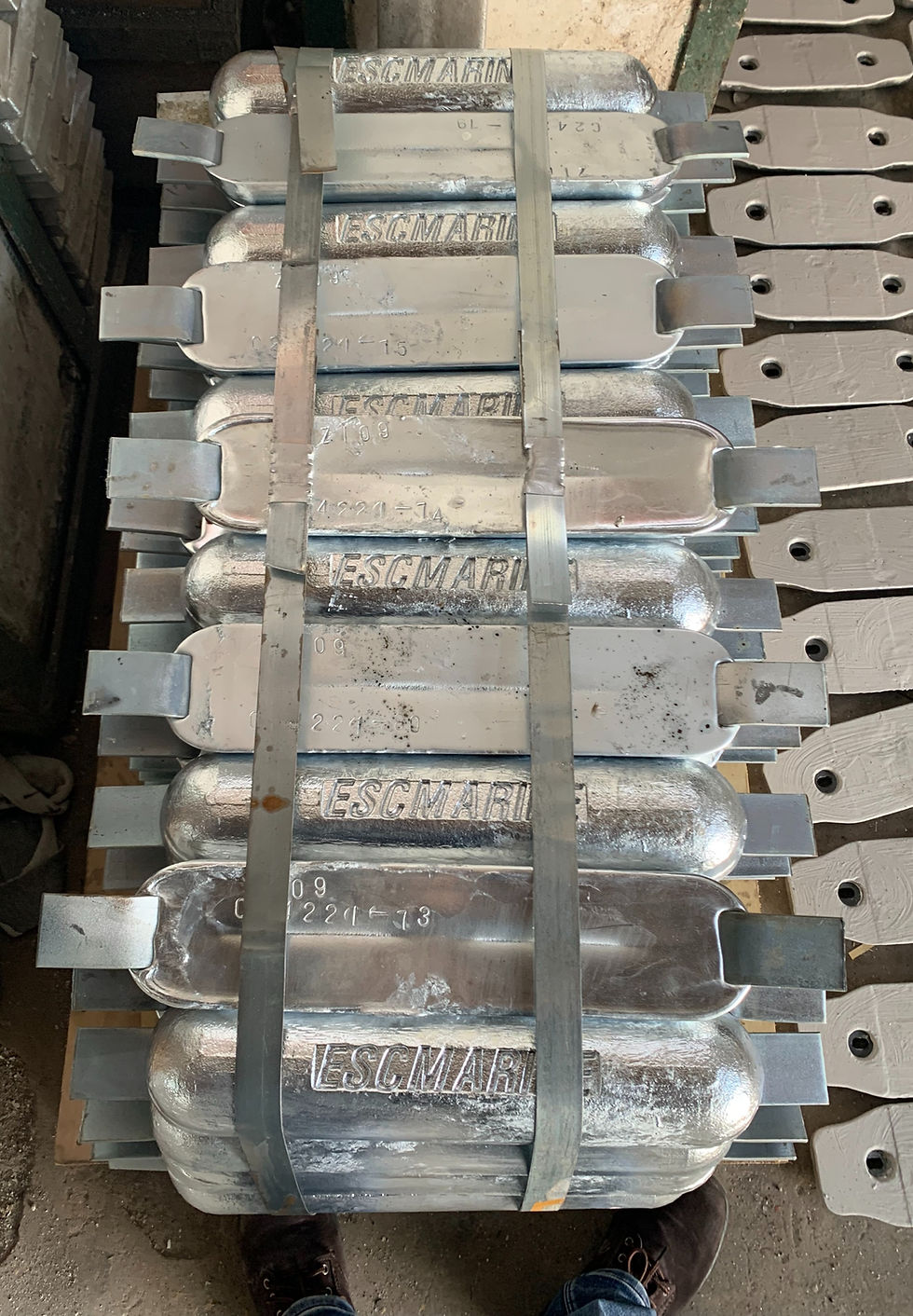
Flat or block. Usually used in flat or relatively flat surfaces like the hull of a ship.
Droplet shaped. These anodes are used to minimize water resistance while cruising.
Cylindrical or bracelet. They are used to provide protection for ship’s pipelines, propeller shafts, and other parts which are circular in cross section.
Tubular. These anode types are used to give protection to cables.
Anode Size
The size of individual anodes depends on the following design factors:
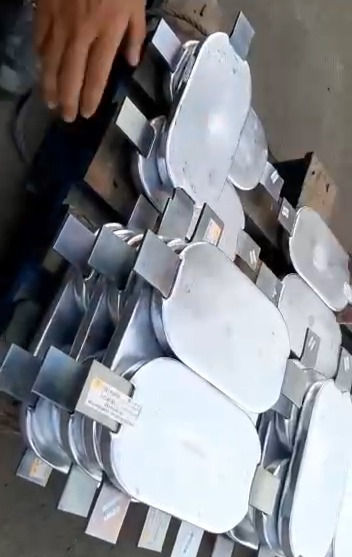
Size and shape of the part to be protected. The hull of ship or boat can accommodate all shapes and sizes of anodes. Smaller parts of a vessel in contrary such as the steering rudder can only take small ones.
Space and Access. While ballast tanks are spacious or bilge keels are easy to access, there are areas in the ship where it is more difficult to perform installation. The bow thruster location is an example.
External factors. Bulky anodes attached to the outside body of a boat or ship can increase resistance against smooth streamlining.
Anode Mounting Technique

Anodes are mounted to protected parts basically in two ways:
Flush-mounted anodes. In this method, the insert or holder is positioned in a manner that the anode body can rest flat or in direct contact with the protected metal surface. The anode insert which is commonly a flat bar is secured by bolt or welding.
Advantage: Flush anodes are more synchronized to the vessel’s geometry and have lower effect on resistance and drag properties.
Disadvantage: They are only 80% utilized throughout their lifespan.
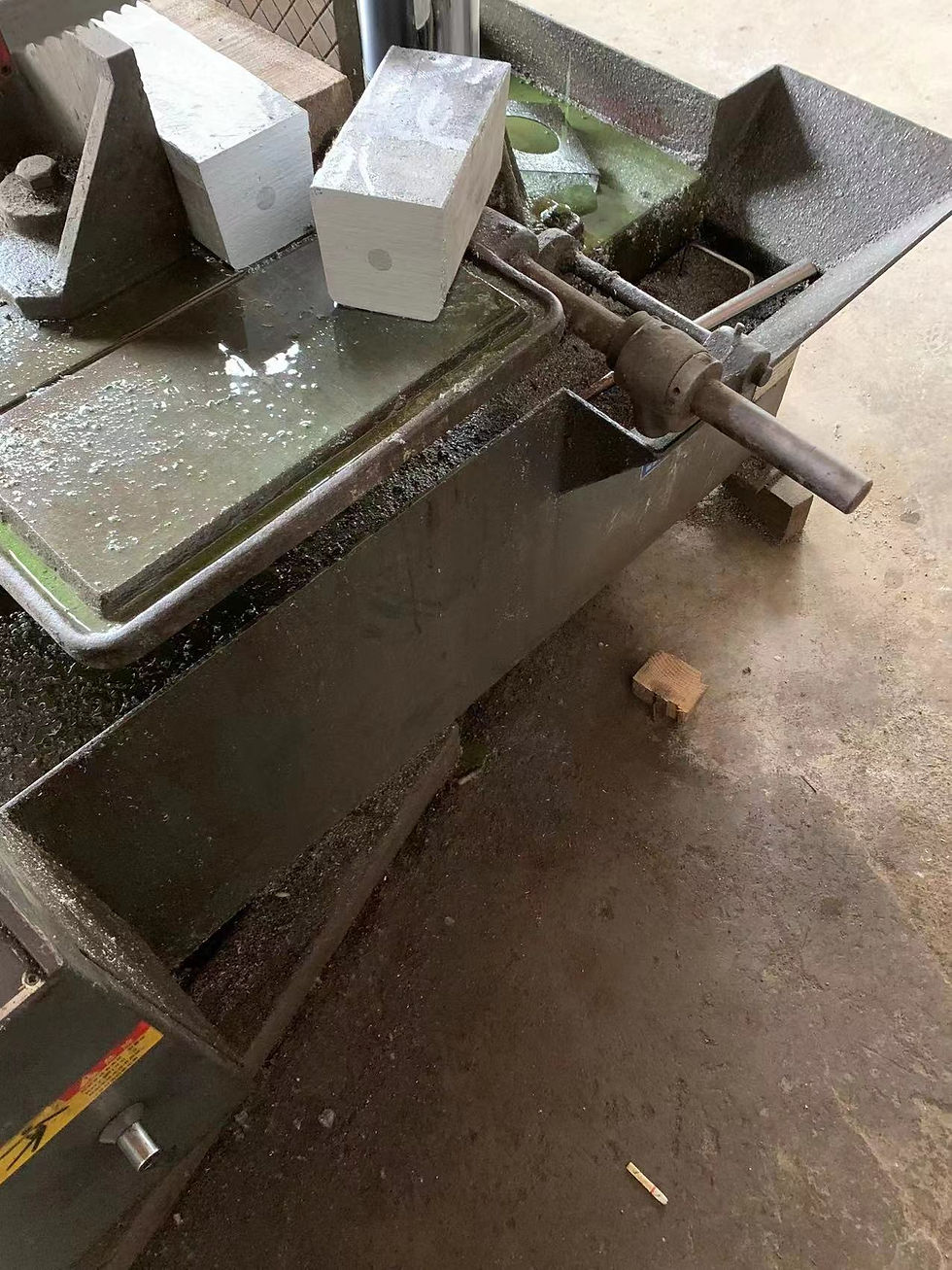
Stand-off anodes. This type of mounting creates space between the anode body and the protected surface. The anode holder becomes more of a leg that makes the anode protruding like a grab bar.
Advantage: Stand-off anodes has better utilization of about 90%
Disadvantage: Due to protrusion, they create more resistance to streamlining and steering
Anode Design, Installation, and Commissioning by ESC
Let our anodes give, and your ships will live!
ESC is capable of selecting specifications and calculating anode quantities depending on site conditions, steel components, and coating systems. Full calculations and drawings to DNV, NACE or BS EN standards alongside project specific standards can be produced by our Corrosion Engineers.
ESC has many years of successful experience and can provide a full suite of items, such as reference electrodes, test points, mounting brackets, bolts, wiring and more.
Please visit us at www.escsteelphil.com , it’s our pleasure to give competitive quotations.
